2.2.2 温度和搅拌速度的影响
实验中选用的有机溶剂二氯甲烷的沸点为 40.1°C,溶剂蒸发时体系的温度决定了挥发速度。实验证明,当制备温度高于溶剂沸点时,体系反应剧烈而使粘度迅速变大,壁材易聚集成片状物、团状物析出。降低蒸发温度延长成囊时间将会得到粒状的微胶囊,因此,实验中采用常温自然蒸发有机溶剂[10]。
从动力学稳定的O/W乳液中获得小粒径胶囊,需要高的能量输入,高速搅拌是一种途径[11], 本实验选用300,500,700和900 r/min不同转速下 制备微胶囊。在显微镜下观察其表面形貌如图4所 示,并进行粒径统计结果如图5所示。结果表明,当 搅拌速度为300 r/min时,所得微胶囊形状不规则, 并且粒子很大,如图4(a)(×1 200)所示。搅拌速度 提高后所得微胶囊为规则的球形,如图4(b~d) (×10 000)所示。从图5可以看出不同速度下的粒径分布情况:900 r/min下0.14~0.89μm,700 r/min下为0.58~1.98μm,500 r/min下为0.94~ 0.78μm,300 r/min下为1.42~1.96μm,随着乳 化速度的提高,粒径变小并且均匀,粒径分布变窄。但是速度过大会破坏乳化形成的胶束的稳定性,从而使芯材周围不能形成完整的囊壳。
2.2.3 芯壁比的影响
在微胶囊化过程中,壁材用量越大,形成的胶囊壁膜越厚,微胶囊的粒径相应增大,并且在使用时破囊所需的能量也会增大;壁材用量太少不能很好地包覆芯材而且会影响微胶囊的储存性。本文选用不同的比例进行实验,结果表明,当芯壁比大于2 ∶1或者小于1∶2时不能很好地包覆。图6显示聚乙烯醇浓度为8%、乳化转速900 r/min时芯壁比为 2∶1,1∶1,1∶2的微胶囊电镜照片。
从SEM照片可以看出,当芯壁比为1∶2时,微胶囊表面不连续,有部分凹陷,可以看出壁材的 含量相对较少;而图6(a,b)的微胶囊光滑且致密。结合图7粒径分布,芯壁比为1∶1时粒径分布很 窄,在0.14~0.89μm之间;芯壁比为2∶1时粒径 分布相对较宽,在1.32~9.47μm之间。考虑到壁材较厚时不容易破坏而影响芯材的使用,本文选用芯壁比为1∶1制备微胶囊固化剂。
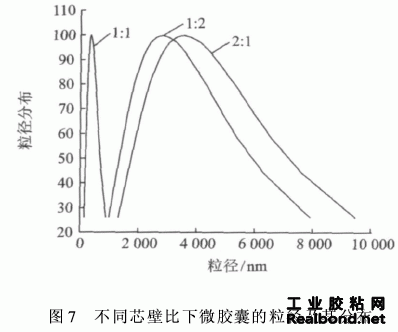
3 结束语
利用溶剂蒸发法成功地制备环氧树脂微胶囊固化剂,通过各种工艺条件下微胶囊表面形貌和粒径大小及其分布的影响,表面活性剂浓度选择8%, 乳化转速选择900 r/min,芯壁比为1∶1时可以制备表面光滑致密、平均粒径1μm之内且粒径分布比较窄的微胶囊。将其与环氧树脂混合后可以使树脂在室温下稳定储存,微胶囊固化剂的固化性能及其固化后对树脂性能的影响将是进一步研究的重 点。