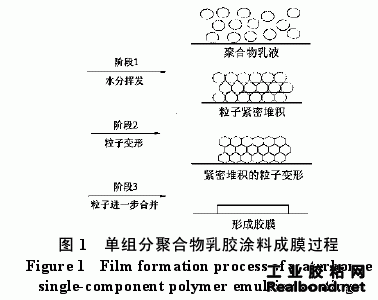
2.2水性环氧涂料的成膜及其与乳胶涂料、溶剂型环氧涂料成膜过程的比较
水性环氧树脂是O/W乳化体系,环氧树脂以乳胶微粒的形式分散在水中,是多相分散体系。当环氧树脂与固化剂(通常是水溶性的胺、聚酰胺等)混合后,固化剂溶解在水相中,其成膜过程可用图2表示[6]。
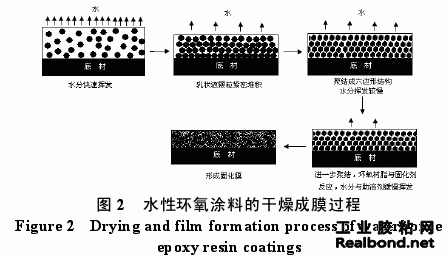
水性环氧涂料涂覆后,在适宜的条件下,水分很快挥发,大部分水分挥发后,分散相微粒相互靠近,形成紧密堆积,残存少量的水填充在乳胶微粒的缝隙间,形成巨大的毛细管压力,相互靠近、堆积的乳胶微粒在毛细管压力下变形成六边形结构。与单组分聚合物乳胶涂料一样,环氧树脂以及部分固化了的环氧树脂在乳胶粒子间相互扩散,直至形成均一、连续的涂膜。与单组分乳胶涂料不同的是,在水分挥发、粒子变形、粒子合并阶段都伴随着环氧树脂与固化剂之间的化学反应。因此,水性环氧体系的固化过程中,物理过程与化学反应交织进行,是一个典型的物理化学过程。在固化成膜过程中,固化剂分子首先和环氧树脂 分散相粒子的表面接触并在表面发生固化反应。随着交联反应的进行,环氧树脂分散相的分子量和玻璃化 温度逐渐提高,使固化剂分子向环氧树脂分散相粒子 内部的扩散速度逐渐变慢,这意味着环氧树脂分散相粒子内部进行的固化反应较其表面的少,内部交联密度也较低。同时,随着固化反应的进行,环氧树脂分 散相粒子逐渐变硬,粒子之间相互凝结成膜的难度加 大。A.Wegmann [6] 认为,水性环氧树脂涂料同溶剂型环氧树脂涂料相比,很难形成均相、完全固化的涂膜,并认为这是影响水性环氧树脂涂膜性能的首要原因。笔者的研究表明,应用合适的工艺得到细腻稳定的环氧树脂乳液体系,并选择合适的固化剂,在适宜的固化条件下仍然能够得到防腐性能、物理机械性能 等综合性能优良的水性环氧树脂涂膜,但与溶剂型环氧树脂涂膜相比,仍然存在一定的差距[ 7-8]。
3.影响水性环氧涂料成膜过程的因素
环氧树脂与固化剂之间的反应场所为乳胶粒子/水 的界面以及乳胶粒内部,固化剂与环氧树脂之间的固化反应速率由固化剂的扩散过程控制[9]。乳胶粒的大小,乳胶粒的界面黏度,环氧树脂的玻璃化温度,环氧树脂与固化剂的相容性等对水性环氧树脂的固化成膜有很大的影响。
3.1分散相粒径对水性环氧涂料成膜过程的影响
乳胶粒的大小对固化成膜过程的影响如图3所示[6]。
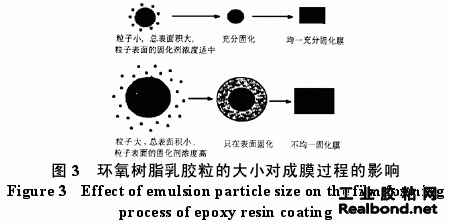
固化剂与环氧树脂的固化反应首先从乳胶粒界面开始,完全反应则需要透过界面膜进入到乳胶粒内部。乳胶粒粒径较小时,乳胶粒具有较大的比表面积,按比例配合的固化剂在乳胶粒表面的分布浓度较低,固化反应速率相对较慢,固化剂有充分的时间与空间扩散进入乳胶粒内部与环氧树脂进行固化反应。因此, 能够形成均一的、固化完全的硬膜。相反,乳胶粒粒径较大时,乳胶粒的比表面积相对较小,固化剂在乳胶粒表面的浓度相对较高,乳胶粒表面快速固化。随 着固化的进行,界面壳层变硬从而阻止了固化剂进一 步向乳胶粒内部扩散,导致乳胶粒内部固化不完全,形成的涂膜物理化学性能下降,主要表现在涂膜的光泽度、硬度降低,涂层的渗透性增高,耐水性、耐化学品性下降,干燥时间延长。涂膜与涂料的性能与分散相粒径的关系如图4所示 [10]。