1·3 TDI的影响因素
1·3·1 蒸馏温度对分离TDI的影响
第二次蒸馏进料速率为1·0 kg/h,进料温度控制在110℃,蒸发面温度在170~200℃之间变 化,绝压不变,保持在40 Pa,每次蒸馏的蒸发面温度不变。将二次蒸余物在105℃保温,待二次蒸馏完成后,加入100℃计量好的醋酸丁酯稀释至75%(wt)的固含量,然后送样分析TDI含量。图1是残余TDI含量随二次蒸馏温度的变化情况。

1·3·2 蒸馏绝压对分离TDI的影响
第一次进料速度控制在1·0 kg/h,刮板转速均固定在150 r/min,进料温度控制在100℃,蒸馏 时控制温度为150℃,第一次蒸馏绝压为5 000 Pa,二次进料温度为110℃,二次蒸馏温度为200℃,变化二次蒸馏的压力进行蒸馏。图2是对于采用不同的压力进行蒸馏,绝对压力对分离TDI的影响情况。从图2中可以看出,绝压越小, 残余TDI含量越低。

1·3·3 刮板转速对分离TDI的影响
第一次进料速度控制在1·0 kg/h,刮板转速均固定在150 r/min,进料温度控制在100℃,蒸馏时控制温度为150℃,第一次蒸馏绝压为5000 Pa,二次进料温度为110℃,二次蒸馏温度为200℃,二次蒸馏压力控制在40Pa,变化刮板转速进行蒸馏。其结果见图3,可见刮板转速越快, 分离效果越好。
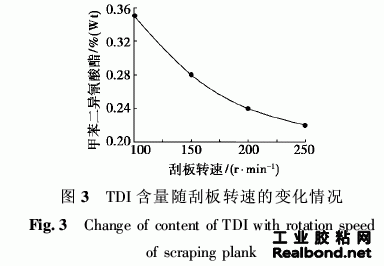
1·3·4 进料速率对分离TDI的影响
蒸馏的进料速率变化,但两次进料速率一样, 蒸馏两次刮板转速都固定在150 r/min,一次进料 温度控制在100℃,二次进料温度控制在110℃,一次蒸馏控制温度为150℃,二次蒸馏控制温度 为200℃,一次蒸馏的绝压均控制在5 000 Pa,二 次蒸馏绝压控制在40 Pa,图4是二次进料速率对分离TDI的影响情况。从图4中可以看出,进料速率越小,残余的TDI含量越低,这是符合一般规律的,因为进料量越大,液膜越厚,表面更新就越慢,TDI就越不容易从液相主体进入气液相界面, 一旦TDI进入液相界面,就很容易分离出来。从上面残余TDI量的数值可看出,其值逐渐变小,但变化幅度又不是很大,可认为用薄膜蒸发器分离TDI液相传质是主要的控制步骤。从图4可以看 出NCO含量随流量的减小而减小,从趋势看,减幅较大。
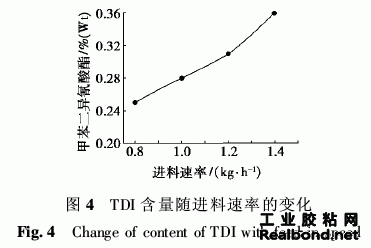
1·4 传质半经验模型建立与求解
短程蒸馏传质和传热模型建立起来很复 杂[3-5],当物性数据不足时,求解非常困难。对于 聚氨酯固化剂这种高粘度的物性体系,在求解的 过程中没有物性数据而无法运算下去(没有TD TMP固化剂在无溶剂情况下的物性数据)。为此 我们需要更简单的计算方法为中试设计提供计算依据。为了使计算方便,先对分离TDI的过程进行分析,在蒸馏TDI之前要先将溶剂蒸馏完,所以在二次蒸馏时,只是蒸馏TDI。由于TDI的浓度不是很大,热量不是很多,液体粘度又很大,流速很慢,加上液膜较薄,还有刮板扰动液膜加速传热,所以可以认为液膜和蒸发壁面温度一致。一般来说,P0-P越大,传质的推动力越大,但P并不是蒸发器真实的压力,而是未凝气体的压力,所以真实的传质推动力要比P0-P值小,将推动力