刘慧森1,2,黄新建2,张海涛1,应卫勇1
(1·华东理工大学化工学院,上海200237; 2·巴陵化工有限公司,湖南岳阳414014)
摘要:利用二氯丙烷混合副产物合成了环氧树脂固化剂,得出了适宜的反应条件;对所生产的固化剂的各种应用性能和应用范围进行了讨论。
关键词:环氧树脂;固化剂;二氯丙烷混合物
中图分类号:TQ314·256 文献标识码:A 文章编号:1002-7432(2004)01-0010-04
1 前 言
环氧树脂具有许多独特的优异性能,在热固性树脂中其综合性能较好,因而发展较快,应用很广。设计最佳材料配方是环氧树脂应用的技术关键。要开发和生产所需性能的环氧材料,就必须设计出相应的专用最佳配方及其成型工艺条件。在环氧树脂的应用中,固化剂占有十分重要的位置。开发新型固化剂比开发新型环氧树脂更为重要,因为文献上发表的一些树脂,有的只有学术价值,没有实际意义。而开发一种新型固化剂,则可以解决环氧树脂应用中的问题。在目前Shell、 Dow、Ciba以及日本几家公司正加紧对中国环氧树脂消费市场抢占、渗透的情况下,国内厂家面临着极为严峻的挑战[1]。根据业内统计, 2002年中国 大陆环氧树脂消费量在296 kt左右,国内企业生产量约为90 kt,占市场份额的30%。造成国内环氧树脂这种现状的主要原因除了产品质量差,品种单一外,主要是环氧树脂和固化剂的配套发展水平低。国外环氧树脂企业十分重视环氧树脂与固化剂的配套生产和销售,每一种环氧树脂都有与之配套 的固化剂。与之相比,国内的环氧树脂配套生产和销售还处于起步阶段,没有一家环氧树脂生产企业能够像国外企业那样实现配套化生产和销售。国内外对用二氯丙烷混合副产物DD混剂的应用和二氯丙烷胺化生产丙二胺进行了研究[2~5]。本文利用环氧氯丙烷生产装置的副产物DD混剂, 胺化后生产环氧树脂行业所需要的线性大分子多胺,一方面可以配套环氧树脂的销售,另一方面可以解决生产装置副产物外销困难而产生的二次污染问题。
2 实验部分
2·1 主要原材料
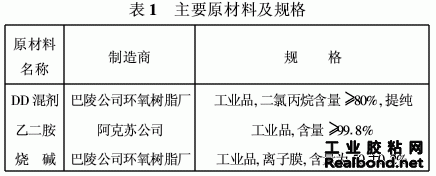
2·2 实验工艺流程
胺化实验工艺流程如下所示。
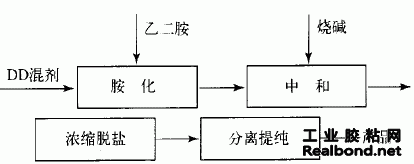
2·3 实验方法
经过计量的DD混剂和乙二胺被加入到胺化反应釜,搅拌升温,达到设定反应温度后,反应3~ 4h,待胺化反应完毕,加入计量好的烧碱,进行中和反应1 h,中和反应完毕后,将反应液移到蒸馏瓶,进行浓缩,脱出大部分的水,然后进行过滤脱盐,滤液进入蒸胺装置进行分离提纯,即得产品。
2·4 分析仪器
气相色谱/质谱联用仪SP6890-5973,色谱柱HP-5MS;同轴双圆筒旋转粘度计NDJ-1粘度 计;凝胶时间测定仪JSQ0801;热机械分析仪 (Thermomechanical analyzen, TMA)。
3 结果与讨论
3·1 多胺固化剂的合成
3·1·1 反应温度和反应时间对DD混剂转化率的 影响
实验中所选择的胺化反应条件为:
原料n(DD混剂)∶n(乙二胺)=1∶4
DD混剂 500 mL
乙二胺 1330 mL
反应温度范围 110~140℃
反应时间 1~4 h
实验结果见图1。
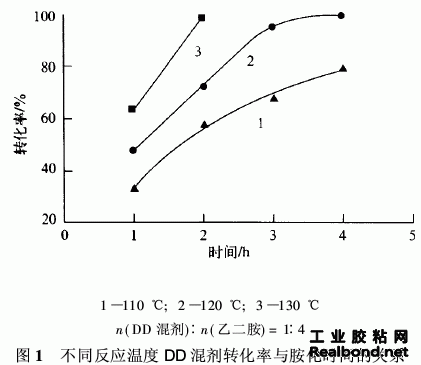
由图1可知,当反应温度120℃,反应时间约 3·5 h时, DD混剂的转化率几乎可以达到100%; 反应温度为130℃和140℃时,反应速度很快, DD混剂的转化率很快就可以达到100%。但是, 同时可以观察到,系统压力上升很高:反应温度为 130℃,反应时间3 h,系统压力达到0·58 MPa; 而反应温度为140℃,反应时间3 h,系统压力达 到0·88 MPa。这可能是反应温度的上升,加剧了 二氯丙烷脱氯化氢副反应,生成2-氯丙烯(沸点 22℃)和1-氯丙烯(沸点32℃)的缘故。
因此,为了抑制二氯丙烷脱氯化氢的副反应的发 生,利用DD混剂生产多胺固化剂的胺化反应的反应 条件应该选择反应温度120℃,反应时间3·5 h。
3·1·2 原料配比对胺化反应的影响
本实验的反应条件如下:原料n(DD混剂)∶n (乙二胺)=1∶1~1∶4; DD混剂500 mL;乙二胺分 别为330、660、1000、1330mL;反应温度120 ℃,反应时间1~4 h。
原料配比对DD混剂转化率的影响关系如图2,原料配比对系统压力的影响如表2。
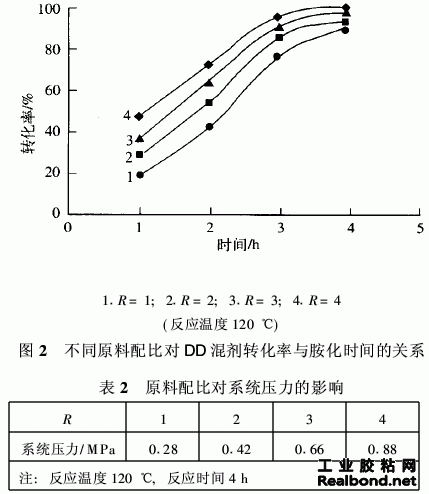
由图2可见, DD混剂和乙二胺所进行的胺化 反应和胺化剂乙二胺的浓度有关,乙二胺的浓度越 高,反应速度越快;从上面对双分子亲核取代反应 历程的分析可以判断出: DD混剂和乙二胺所进行 的胺化反应历程为双分子亲核取代反应历程。
由表2可见,系统压力和乙二胺的浓度有关, 乙二胺的浓度越大,系统压力越高。前面已经分 析,系统压力的升高,是由于胺化反应的同时,产 生了副反应:二氯丙烷在碱性条件下发生了脱氯化 氢的反应,生成低沸点的1-氯丙烯和2-氯丙烯 的缘故。这说明乙二胺的浓度越大,脱氯化氢的副 反应越剧烈;同样从上面对双分子消除反应历程的 分析可以判断出:脱氯化氢的副反应历程为双分子 消除反应历程。
3·1·3 原料配比对产物组分分布的影响
设定反应温度为120℃,反应时间3·5 h,在1∶1和1∶4范围内调整DD混剂和乙二胺的物质的量比,考察原料配比对产物组分分布的影响,如表 3。
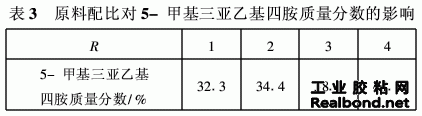
由表3可见,调整原料配比可以调整固化剂的 组分分布,这说明该工艺路线可以通过调整原料配 比来达到生产所需要的多亚乙基多胺的目的:增加 乙二胺的摩尔比,有利于生成大分子质量的线性脂 肪族多胺,当然为了控制生产成本,乙二胺的过量 应该有一定的控制,一般来说,控制DD混剂对乙 二胺的物质的量比为1∶4是合适的。但是本实验的 结果和文献[5]所报道的51%的收率还有一定的差 距,这可能是因为本实验使用的是DD混剂而不是 二氯丙烷的原因。
3·2 应用实验
3·2·1 胺值和粘度
原料配比采用n(DD混剂)∶n(乙二胺)=1∶4 反应温度120℃,反应时间3·5 h,由以上工艺条 件所得的产品命名为CA,分别进行胺值和粘度的 测定,其结果和乙二胺相应指标进行比较,结果见表4。
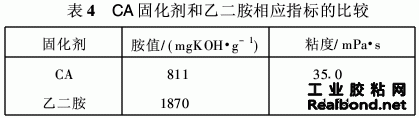
由表4可见, CA固化剂较乙二胺的胺值有大幅 度的降低,说明CA固化剂的分子质量较乙二胺有 较大程度的提高,相应地,其活性也应该下降。因 此,在施工过程中, CA固化剂和环氧树脂的配料比 例可以提高,固化反应的放热相对较少,可以防止 环氧树脂的爆聚而影响环氧材料的力学性能,有利 于实际应用; CA固化剂的粘度较乙二胺的粘度大, 这是合理的,因为CA固化剂中的多胺都是大分子 线形多胺。但是, CA固化剂粘度的提高还不足以对 施工操作条件产生影响,因为一般液体环氧树脂的 粘度比它大得多,一般多在10 Pa·s以上。
3·2·2 放热曲线
固化系统:环氧树脂CYD-128, CA固化剂。
实验结果如图3。
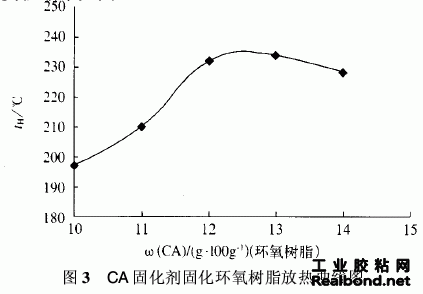
由图3可见, CA固化剂的用量对固化反应的影响很大,固化剂不足或过量,固化物的性能都不能达到最好;同时也可以看出: CA固化剂对CYD -128环氧树脂的最佳用量约为12·7%。
3·2·3 凝胶时间
固化系统:环氧树脂CYD-128, CA固化剂。 分别测定其温度为10℃、25℃、30℃、40℃时的凝胶时间,和二亚乙基三胺进行比较,其结果见 表5。
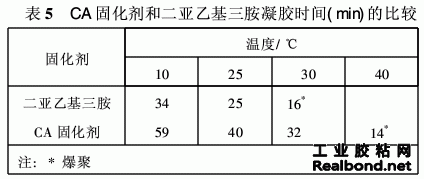
由表5可见,和二亚乙基三胺相比, CA固化 剂的凝胶时间有一定程度的延长,这对于实际应用 是有益的。但是在常温(25℃)下, CA固化剂的凝 胶时间也只有40 min,说明其活性还是很大,还 可以进一步降低。
3·2·4 玻璃化转变温度
CYD-128环氧树脂和CA固化剂作成样条,常温固化1周。
通过TMA测定样条的玻璃化转变温度约为93 ℃。同其它类型固化剂相比, CA固化剂固化的环氧材料的耐热性稍差,一般来说,可以应用于涂料和胶粘剂行业。
3·2·5 剪切强度
CYD-128环氧树脂、CA固化剂体系固化48 h,剪切强度为12·3 MPa。
可以看出: CA固化剂固化的环氧树脂固化物的剪切强度相对偏低。这是因为CA固化剂为胺类固化剂,固化温度相对较低,和环氧树脂的固化物的交联密度相应较低。
4 结 论
a·利用DD混剂生产环氧树脂多胺固化剂,其 工艺可行;
b·DD混剂和乙二胺所进行的胺化反应 过程中, DD混剂的转化率和胺化剂乙二胺的浓度有关,乙二胺的浓度越高, DD混剂的转化率越大;
c. DD混剂和乙二胺所进行的胺化反应历程为 双分子亲核取代反应历程;
d·DD混剂和乙二胺所 进行胺化反应的同时所发生的副反应和乙二胺的浓 度有关;乙二胺的浓度越大,脱氯化氢的副反应越剧烈;
e.脱氯化氢的副反应的反应历程为双分子消除反应历程;
f·为了得到高含量的线性大分子脂肪族多胺,提高原料配比中乙二胺的含量是有益的;
g·综合权衡,适宜的胺化反应条件为:反应温度120℃,反应时间3·5 h,原料配比n(DD混剂)∶n(乙二胺)=1∶4;
h.所得到多胺固化剂属于 常温固化剂,和CYD-128环氧树脂配胶,其最佳 用量为12·7%;在常温下固化,凝胶时间约为40 min;玻璃化转变温度约为93℃;剪切强度为 12·3 MPa;该固化剂的应用性能和多亚乙基多胺 固化剂相似,适合应用于涂料与胶粘剂行业。
参考文献:
[1]蒋钧荣.国内外环氧树脂发展概况[J].热固性树脂, 2002, 17 (4): 22-25.
[2]张建国,曹正祥.二氯丙烷氨化合成丙二胺的开发和应用 [J].化工科技市场, 2000, (4): 14-15.
[3]沈海琴.环氧丙烷生产中副产物1, 2-二氯丙烷的综合利用 [J].化学推进剂与高分子材料, 1998, (3): 5-9.
[4]高旭东,李辉,王忠贤.由1, 2-二氯丙烷合成1, 2-丙二 醇的方法[J].氯碱工业, 2000, (5): 20-22.
[5] CA 109 39720d.